The Art and Science of Wood Processing: Techniques That Transform Timber into Treasures
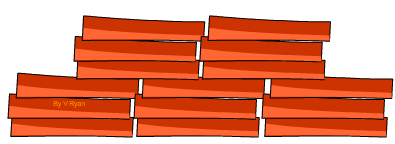
Introduction to Wood Processing;
Wood is more than just a material; it’s a canvas for creativity and craftsmanship. From the sturdy beams of ancient structures to the intricate carvings found in handmade furniture, wood has been an essential part of human civilization. The journey from raw timber to functional art involves both artistry and science—a blend that transforms simple logs into cherished treasures.
As we delve into the world of wood processing, you’ll discover techniques that have evolved over centuries, adapting to changes in technology and design preferences. Whether you’re a seasoned craftsman or simply curious about what goes on behind the scenes, this exploration promises insights into how various methods breathe life into timber. Join us as we unravel this fascinating craft!
History and Evolution of Wood Processing Techniques;
Wood processing has roots that stretch back to ancient civilizations. Early humans recognized the utility of timber, crafting basic tools and shelters from fallen branches and trunks. As societies evolved, so did their techniques.
The Egyptians pioneered methods for shaping wood into furniture and boats, using simple hand tools. The Greeks refined these skills with advanced joinery techniques, setting standards that influenced craftsmanship across generations. During the Middle Ages, sawmills emerged, revolutionizing timber production. These innovations laid the groundwork for modern woodworking practices.
The Industrial Revolution further transformed wood processing with mechanization. Power saws replaced hand tools, increasing efficiency and output significantly. Today’s woodworkers blend traditional methods with cutting-edge technology. CNC machines allow for precision while artisans continue to celebrate age-old techniques in their creations. This ongoing evolution highlights our enduring relationship with this remarkable natural resource.
Types of Wood Used in Processing;
Wood species play a crucial role in the processing landscape. Each type offers unique characteristics that dictate its suitability for various applications. Wood processing is a complex and fascinating process that involves transforming raw timber into a variety of useful and beautiful products. One crucial aspect of wood processing is the type of wood used, as different types of wood possess unique properties that can affect the result. In this section, we will explore some of the most commonly used types of wood in the process.
1. Hardwoods
Hardwood is one of the most popular woods used in wood processing due to its durability and strength. It comes from deciduous trees such as oak, maple, cherry, and walnut, which are slow-growing compared to softwood trees. This slow growth results in tighter grain patterns, making hardwoods denser and more resistant to wear and tear. Hardwoods are often used for furniture making, flooring, cabinetry, and decorative pieces due to their attractive appearance and long-lasting nature.
2. Softwoods
Softwood comes from coniferous trees like pine, fir, spruce, or cedar. Unlike hardwoods, softwoods grow at a faster rate resulting in larger pores within the wood fibers. This makes it less dense but also more pliable than hardwoods. Softwoods are widely utilized in construction projects because they are easy to work with and readily available.
3. Engineered Wood
Engineered wood is a relatively new addition to the world of wood processing but has gained immense popularity due to its versatility and cost-effectiveness. It consists of layers or strands of real wood pressed together with adhesives under high pressure to create strong boards suitable for various applications such as furniture-making or structural components for buildings.
4. Wood Composites
Wood composites refer to manufactured boards made by binding together smaller pieces or particles of real wood using adhesives or resins under high pressure. These include medium-density fiberboard (MDF), particleboard (PB), oriented strand board (OSB), laminated veneer lumber (LVL), and many others. These composite woods are often used in construction, furniture-making and even in creative projects like woodturning.
5. Exotic Woods
Exotic woods refer to species of trees that are not native to the region where they are being processed. These types of wood offer unique colours, patterns, and textures, making them highly sought after by artisans and craftsmen for decorative purposes. Some examples include African mahogany, Brazilian cherry, or teakwood.
Understanding the different types of wood used in processing is crucial as it can greatly impact the final product’s quality and characteristics. Each type of wood has its unique properties that make it suitable for specific applications; however, some may require special tools or techniques during processing due to their density or hardness levels. As a consumer, knowing the various types of wood used in processing can help you make informed decisions when purchasing wooden products or embarking on your woodworking projects.
Preparing and Sorting Timber for Processing;
Preparing and sorting timber is a crucial step in the wood processing journey. It sets the foundation for quality craftsmanship. First, logs are inspected to determine their species and grade. This helps identify the best use for each piece of wood. Some may be perfect for furniture, while others might serve better as structural components.
Once sorted, logs undergo debarking to remove outer layers. This not only enhances appearance but also eliminates pests that could compromise integrity. Next comes cutting into manageable lengths based on intended projects. Precision at this stage ensures minimal waste and optimal results later on.
Proper storage is equally essential; keeping timber stacked in a dry environment prevents warping or decay. Each piece deserves careful handling to maintain its unique qualities before it transforms into something extraordinary.
Techniques for Cutting, Shaping, and Joining Wood;
Cutting, shaping, and joining wood are fundamental processes in woodworking that require precision and skill. Each technique plays a crucial role in turning raw timber into functional art.
- For cutting, saws come in various forms—table saws, band saws, and mitre saws. Each has its purpose, allowing for straight cuts or intricate designs. The choice of blade can also affect the quality of the cut.
- Shaping involves tools like chisels and routers to create curves or decorative edges. This step elevates a simple plank into something visually captivating.
- Joining techniques are essential for constructing sturdy pieces. Mortise-and-tenon joints provide strength while dovetails add beauty and craftsmanship. Wood glue often complements these methods, ensuring durability over time.
Each technique showcases the balance between artistry and functionality. It’s this blend that transforms ordinary wood into remarkable creations ready to be enjoyed by all.
Finishing and Protecting Wood Products;
Finishing wood products enhances their beauty and longevity. The right finish can elevate the natural grain, adding depth to each piece. There are various types of finishes available — oils, stains, varnishes, and lacquers. Each serves a unique purpose in protecting the wood from moisture and wear while providing aesthetic appeal.
Applying an oil finish penetrates deep into the fibres, nourishing the wood while offering a subtle sheen. Stains allow for colour customization without obscuring the grain’s character. For those seeking durability, varnishes create a hard protective layer that withstands scratches and UV damage. Lacquer dries quickly but requires careful application due to its strong fumes.
Proper preparation is key before finishing begins. Sanding surfaces smoothly ensures even application and helps prevent imperfections from marring your masterpiece. Lastly, regular maintenance prolongs life after finishing. Simple cleaning routines keep wooden items looking fresh for years to come.
Innovative Wood Processing Methods;
Advancements in technology have sparked a revolution in wood processing methods. Traditional techniques still hold value, but innovation has introduced exciting possibilities.
One noteworthy method is CNC machining. This computer-controlled technology allows for the precision cutting and shaping of wood into intricate designs that were once impossible to achieve by hand. Another fascinating approach is the use of laser engraving. Lasers can create detailed patterns on wooden surfaces with remarkable accuracy, enhancing aesthetic appeal while maintaining structural integrity.
Moreover, 3D printing has begun making waves in the industry. It enables manufacturers to produce complex wooden structures layer by layer, opening doors to unique creations and customized furniture pieces.
Biotechnology also plays a role as researchers explore ways to enhance wood properties through microbial treatments or enzymatic processes. These methods not only improve durability but also contribute to sustainable practices within the sector.
The Artistry of Handmade Wooden Items;
Handmade wooden items embody a unique charm that mass-produced products often lack. Each piece tells its own story, influenced by the wood’s grain, colour, and texture. Artisans pour their skills and creativity into every cut, carve, and finish.
The meticulous attention to detail sets handmade creations apart. Whether it’s a finely crafted bowl or an intricately designed chair, the imperfections become part of its beauty. They are reminders of the human touch behind each item. Sustainability also plays a crucial role in this artistry. Many artisans source timber responsibly and focus on using reclaimed materials whenever possible. This not only honours nature but adds character to each creation.
Customers appreciate the authenticity of handmade wooden pieces. These treasures invite personal connection; they can enhance any space while reflecting individual style and values. The artistry involved goes beyond craftsmanship—it celebrates tradition and innovation harmoniously intertwined.
Future of Wood Processing: Advancements and Challenges
The future of wood processing is an exciting frontier, brimming with advancements that harness technology and innovation. Automation and robotics are taking centre stage, increasing efficiency while reducing labour costs. Smart machinery equipped with AI can now optimize cutting patterns and minimize waste.
Yet, progress doesn’t come without challenges. The industry faces pressure to maintain sustainability amid growing demand for timber products. Adapting to eco-friendly practices is crucial for long-term viability. Another hurdle lies in the skills gap within the workforce. As traditional methods evolve, training programs must keep pace to equip artisans with new techniques alongside time-honoured craftsmanship.
Consumer preferences also play a pivotal role in shaping this landscape. There’s a rising trend toward personalized wooden items, pushing manufacturers to rethink production processes while maintaining quality standards.
Conclusion:
Wood processing is a captivating blend of art and science. It transforms raw timber into functional and beautiful objects that enrich our lives. Each stage, from selecting the right type of wood to applying innovative techniques, reveals the skill and creativity imbued in woodworking.As we navigate through various methods — whether traditional or modern — it’s clear that each piece tells its own story. The craftsmanship involved showcases not only technical prowess but also a deep respect for nature’s resources.
Sustainability continues to play an essential role in this industry. As artisans adopt eco-friendly practices, they ensure that future generations can enjoy the beauty of wood while maintaining ecological balance.Every handcrafted wooden item holds value beyond its practicality; it embodies passion and dedication. This appreciation for both artistry and scientific principles enables us to cherish the treasures created from timber long after they leave the workshop.